Pour bénéficier d’un affichage optimal de la boutique en ligne de PanGas, vous avez besoin pour le navigateur de la version minimale suivante:
• Internet Explorer 9.0
• Mozilla Firefox 38
• Safari 8
• Chrome 45
Veuillez vous assurer que JavaScript est activé dans les paramètres de votre navigateur.
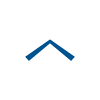
Decarbonization and performance increase
- Home
- Applications
- Metal & Glass
- Glass
- Decarbonization and performance increase
Oxyservice
Efficient production without interruptions. Get everything out of the way now - with our Oxyservice!
Oxyservice from Linde Gas is designed to ensure that furnaces can continue to operate without interruptions. It is a fast, efficient delivery service that contributes to a longer life for furnaces. It also allows producers to continue production during repairs to regenerators or reclaimers by eliminating the need for a heat recovery system.
Oxyservice is the ideal solution for glass melting furnaces
Objectives
- Infestation/damage of regenerators or recuperators
- Increased load on regenerative or recuperative air preheating systems due to tub travel and raw materials
- Increasing duration of hull voyages
- Fluctuating tonnage requirements and utilization of the glass furnace
- Utilization of the glass furnace by more than 100% due to demand/brand development
- Minimization of downtimes and interruptions
- Optimized design of the glass melting tank
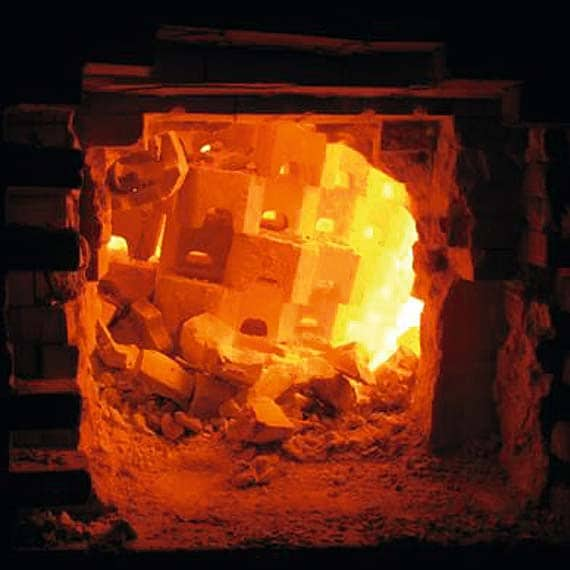
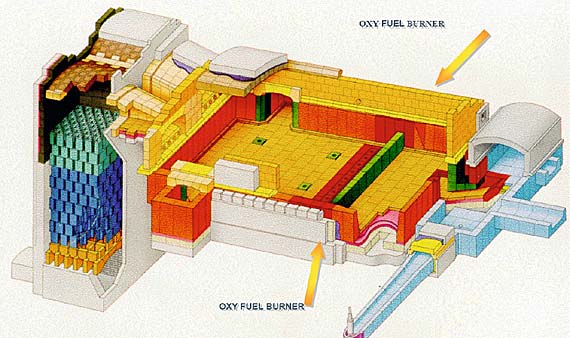
The basic principle of Oxyservice
Oxyservice from Linde combines all the technology needed for the efficient use of oxygen - from delivery to plant operation.
Services
- Engineering in pipeline construction for O2 and natural gas
- Commissioning support
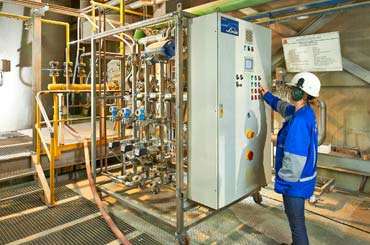
O2 control line
O2 / natural gas control line
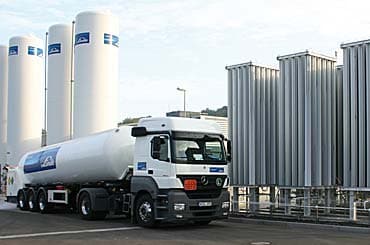
O2 tanks/air evaporator
supply
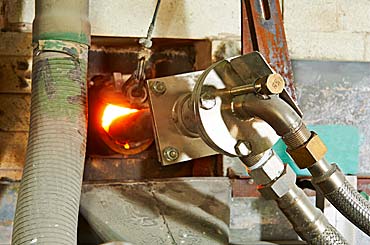
O2 lances
oxygen burners
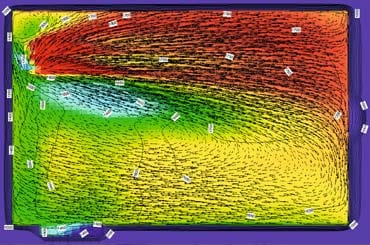
Simulation by means of GS
Benefits of Oxy Service
More flexible, more reliable, more economical
Linde's Oxy Service is based on the activities and experience of the past 10 years.
Benefits
- Flexible maintenance of melting capacity with O2 lances or oxy-fuel burners
- Minimization of production losses due to prolonged furnace movements using oxygen during main and intermediate repairs
- Significant reduction in flue gas/volume of the glass container at the same or higher melting capacity and the same or optimized glass quality
- Reduction of the load on the regenerator/recuperator
- Low investment costs
- One-stop solutions - from O2 enrichment to firing the glass melting tank with fully oxygenated fuels
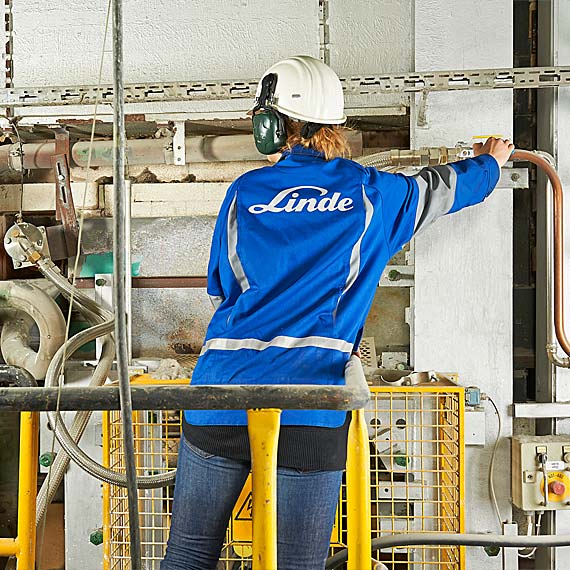
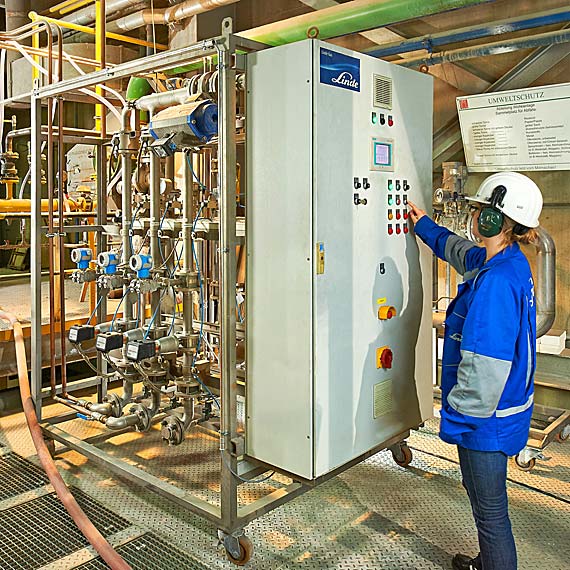
Plant technology
Achieve the best results with customized technology
State-of-the-art plant technology enables optimized production
Available controlled systems
Oxy service systems, O2 control systems
- 1 x 2500 Nm3/h O2
- 1 x 1000 Nm3/h O2
- 1 x 500 Nm3/h O2
Oxyfuel controlled system (pure O2 operation possible)
- 2 x 2 MW natural gas/O2
Oxy-fuel controlled system
- 2 x 2 MW natural gas/O2
- 2 x 3 MW natrual gas/O2
Oxy Service Technology Package - Oxygen Enrichment
Enriching combustion air with oxygen - Less pressure in the furnace, better performance
Furnace operation without Oxy Service
- Cross-fired, regenerative oil/air furnace, container glass
- Tonnage 200 t/day (up to max. 220 t/day)
- Air preheating (before damage to regenerators) approx. 850 °C
Initial situation:
Damage to the horizontal chambers (air preheating at ca. 600-700 °C) and the resulting operation of the furnace led to a greatly increased furnace pressure and reduction of melting capacity by ca. 20% to ca. 165 t/day.
Results with Oxy Service
- Tonnage: 200-205 t/day (approx. 165 t/day + approx. 35 t/day)
- Reduction of the furnace pressure by more than 30
- NOx values of the furnace during O2 maintenance can increase by approx. 5
- Duration: up to 24 months
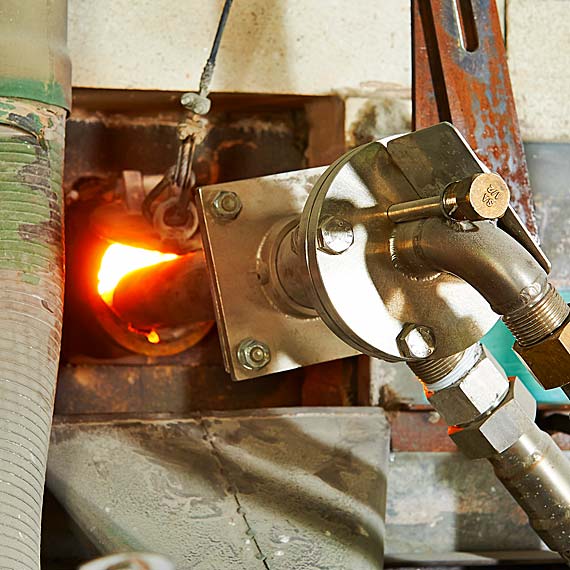
Oxy Service Technology Package - Oxyfuel Burners
Using oxyfuel burners - lower volume flows, higher performance
Initial situation without Oxy Service with burners
- Regenerative gas/air U-flame furnace, container glass
- Tonnage 220 t/day (max. 230 t/day)
- Air preheating (before damage to regenerators)
Approx. 1,100-1,200 °C
Problem:
Damage to regeneration chambers, reduction in air preheating and consequent operation of the furnace lead to a reduction in melting capacity of about 20% to about 160-170 t/day.
Results with Oxy Service
- Tonnage: 200-210 t/day (approx. 160-170 t/day + approx. 30-40 t/day)
- Reduction of volume flows by approx. 20
- NOx values of the vessel during O2 maintenance increased by approx. 5
- Project duration: 18 months
Oxy Service Technology Package - All Oxy Fuel Package
All on kerosene. Stable process, improved glass quality
Initial situation without Oxy Service
- Regenerative gas/air U-flame furnace, container glass
- Tonnage 230 tons/day (70 m2 melting surface)
Task
Maintain a melting capacity of 50% of capacity, equivalent to 115 tons/day, in the U-flame furnace while the regenerators are repaired for 4-6 weeks.
Operation of the U-flame furnace with two oxyfuel burners and an O2 lance at the burner port (use of Oxy Service).
Media operation (one burner port in operation, no changeover):
- COROX®-II (type 3MW) Natural gas 330 Nm3/h Oxygen 380 Nm3/h
- COROX®-II (type 3MW) Natural gas 330 Nm³/h Oxygen 380 Nm3/h0
- O2 lance Oxygen approx. 400 Nm3/h
- No combustion air
Results with Oxy Service
Process stable maintenance of tonnage of 110-115 tons/day of glass melting tank in fully oxygenated condition for 5-6 weeks with improved glass quality.