Pour bénéficier d’un affichage optimal de la boutique en ligne de PanGas, vous avez besoin pour le navigateur de la version minimale suivante:
• Internet Explorer 9.0
• Mozilla Firefox 38
• Safari 8
• Chrome 45
Veuillez vous assurer que JavaScript est activé dans les paramètres de votre navigateur.
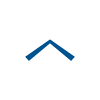
Laser AM & ADDvance® process gases
- Home
- Applications
- Additive Manufacturing (AM)
- Laser AM & ADDvance® process gases
Laser AM & ADDvance® process gases
Fabrication of metal parts with precision, low waste and great design freedom
Additive manufacturing processes using laser technology, such as laser powder bed fusion (L-PBF), laser metal deposition (LMD) and selective laser sintering, are the most widely used 3D printing processes. To fabricate a 3D part layer by layer from metal wire or metal powder, a heat source is used to melt and bond droplets and powder particles together. All of these processes require industrial gases to protect the hot substrate from the atmosphere and to adjust the properties of the components. Linde can ensure that industrial gases and gas management systems meet the specific production requirements.
Laser powder bed fusion (L-PBF) Laser Metal Deposition (LMD) Selective laser sintering
Laser powder bed fusion (L-PBF)
Laser powder bed fusion (L-PBF) is known by several names, such as selective metal laser sintering, metal laser melting, direct metal printing and direct metal laser sintering. Linde supplies the customer with gas supply systems for pure gaseous or liquid argon, creating a suitable inert atmosphere for L-PBF processes.
The following materials are commonly used in laser powder bed fusion (L-PBF) processes:
- Titanium
- Stainless steel
- Maraging steel
- Aluminum
- Cobalt chrome
- Nickel alloys
- Inconel
Linde solutions for L-PBF processes:
- Argon gas supply - design, supply and installation
- Active gas supply - pre-mixed gas mixtures or on-site mixing to ensure process requirements are met
- ADDvanceTM O2 precision - controlled space atmosphere
- On-site support - process and/or technical support
- Online gas management - design and maintenance services
- Gas safety - equipment, safety testing and training
The process
A powerful laser beam scans across a bed of powder. Exposed powder is sintered in the process. A layer of the component is made. The build platform is slightly lowered. Then more powder is added and the laser beam begins to build up the component layer by layer. In this technique, which is suitable for the production of small and precise parts, the atmosphere of the build room must be well protected from harmful impurities.
Laser Metal Deposition (LMD)
Laser Metal Deposition (LMD), also known as "near-net-shape manufacturing," is a process that uses a high-power laser beam connected to a robotic or gantry system to create a molten pool on a metal substrate to which powder or metal wire is fed. Linde provides its customers with gas supply systems for gaseous or cryogenic liquid gases, such as helium, argon or nitrogen, that support the weld build-up welding processes.
Best process gases for LMD and L-PBF processes
- Argon, nitrogen and helium with high purity
- LASGON® mixtures - customized solutions for laser process gases
- In addition, the presence of hydrocarbons and moisture should be avoided
Linde solutions for LMD processes:
- Argon, helium and nitrogen gas supply - design, supply and installation
- Active gas supply - pre-mixed gas mixtures or on-site mixing to ensure process requirements are met
- On-site support - process and/or technical support
- Online gas management system - design and maintenance services
- Gas safety - equipment, safety testing and training
The process
In LMD, the powder is fed into a carrier gas and delivered to the substrate through a nozzle concentric with the laser beam. The laser beam melts the powder particles before they hit the substrate and welds them to the existing part, creating the part layer by layer in this manner. Often a shielding gas is also used to protect the weld area from the ambient air. The method is suitable for larger parts that require a higher application rate. LMD is used in a wide range of applications, such as surface mount and repair welding for the deposition of die surfaces for high-performance components, such as aircraft engine parts and military equipment.
Selective laser sintering
Selective laser sintering (SLS) is a popular process for additive manufacturing that uses polymer powders such as nylon, carbon fibers, fiberglass-reinforced nylon and fine polyamide. Linde provides its customers with cryogenic liquid nitrogen , which supports selective laser sintering processes.
Linde solutions for SLS processes:
- Nitrogen gas supply - design, delivery and installation
- On-site support - process and/or technical support
- Online gas management system - design and maintenance services
- Gas safety - equipment, safety testing and training
- Linde's expertise and service solutions for the additive manufacturing industry
The process
The SLS process begins by heating the polymer powder to just below its melting point. A CO2 laser then sinters the powder in an atmosphere of inert gas. Once the first layer is applied, the build platform sinks and fresh powder is pushed onto the platform. Nitrogen is often used to protect the heated powder and material from reacting with the ambient air.
Thanks to its ability to quickly convert complex CAD geometries into functional prototypes, selective laser sintering is very popular with prototypers and product designers.