Pour bénéficier d’un affichage optimal de la boutique en ligne de PanGas, vous avez besoin pour le navigateur de la version minimale suivante:
• Internet Explorer 9.0
• Mozilla Firefox 38
• Safari 8
• Chrome 45
Veuillez vous assurer que JavaScript est activé dans les paramètres de votre navigateur.
Preheating & postheating
Optimal processes to preserve material properties
Higher strength steels are increasingly being used because this group of materials has the potential to reduce the weight and cost of a structure. These improved properties are particularly beneficial in harsh environments such as offshore wind farms. To achieve optimal results when welding high strength steels and to avoid negatively affecting the material properties, preheating and postheating is usually necessary.
Preheating Heating Hardware LINDOFLAMM® burner Flame straightening & training according to DVS guideline 1145 Flame blasting & training in accordance with DVS guideline 1147
Preheating
Preheating with less time spent without affecting the functionality of the workpiece
High-strength steels are increasingly used because this group of materials offers the possibility of reducing the weight and cost of a structure. Preheating preserves the properties of the material. Preheating is often necessary to maintain the mechanical-technological properties of high-strength steels and effectively prevent defects such as hardening or cracking. This preserves the tensile strength and other properties of the steel. Heat is introduced into the metal with a LINDOFLAMM® torch. The additional energy introduced into the material facilitates the cutting and welding of metals. Preheating is recommended depending on the material and for material thicknesses greater than 25 mm.
Parameters for successful preheating
Preheating is recommended or prescribed by many standards and regulations. However, it can be an extremely complicated operation where the optimal parameters may vary from application to application. Critical factors for successful preheating are accurate temperature control and even heat distribution across the thickness of the material. The preheating temperature depends on the type and thickness of the material, as well as on the welding process and the filler metal used afterwards. Correct temperature measurement is of utmost importance here and requires special care.
Optimizing preheating with acetylene as a fuel gas
For an optimal preheating process, the plant concept must be adapted with regard to the process gases and the equipment used. LINDOFLAMM® burners use exclusively acetylene as fuel gas, as this offers numerous advantages with regard to preheating, such as: highest flame temperature, fastest heat transfer to the component, precise, locally defined heat input into the component, as well as low moisture content in the flue gas stream and thus reduction of the risk of hydrogen-induced cracking.
Accurate temperature measurement during pre-heating
Accurate measurement of the actual preheating temperature immediately before cutting or welding can be problematic and therefore requires great care on the part of the operator. Linde offers several methods to optimize temperature measurement, including temperature-sensitive paint pens and varnishes, mechanical contact thermometers, thermocouples and infrared pyrometers. To automate temperature control, temperature measurement systems can be integrated into LINDOFLAMM® control systems.
The best equipment for preheating: LINDOFLAMM® burners
We know that commercially available standard concepts do not always meet individual requirements. That is why we have developed a range of special burners and nozzles specifically designed for reproducible flame settings and long life. It is with a certain pride that we describe LINDOFLAMM® systems and burners as the best in the entire industry. They can be tuned to maximize thermal efficiency. We have achieved this with sound technical knowledge, research and practical experience.
The benefits at a glance:
- Easy to apply - preservation of material properties
- Allows high quality welding
- Reduces the need for post-processing and post-treatment of workpieces
- Most effective with acetylene as fuel gas: shorter preheating times
- Reduces the risk of hydrogen-induced cracking
- Adaptation of burner selection to customer requirements
- Customized gas supply concepts
- Can be integrated into existing process chains
Complete Linde range for higher strength materials
Our LINDOFLAMM® burners can be integrated into automated systems and offer cost-effective solutions that meet the highest safety standards. Our complete offer ranges from acetylene supply solutions and burners to gas management systems and support services. If you are already performing preheating operations or considering it for future production, please contact our application engineers. They will be happy to show you how the LINDOFLAMM® portfolio can help you improve productivity and quality while reducing costs.
Materials suitable for preheating include:
- Unalloyed and low-alloy steel
- Aluminum and aluminum alloys
- Copper
Heating
Honest technology and in-depth process knowledge - reheating with LINDOFLAMM® torch technology
When using high-strength steels, reheating plays a decisive role in maintaining material properties after welding.
Reheating with LINDOFLAMM® torch technology
When a workpiece is preheated before welding, it often needs to be reheated as well. This process takes place immediately after welding, often with a LINDOFLAMM® torch. The area around the weld is heated to remove residual stresses and diffusible hydrogen. This is often followed by a controlled cooling process that effectively prevents the formation of cold cracks.
When reheating, the optimal process is critical
.Reheating can be a complex operation that requires careful selection of all process parameters. Valuable time and money can be lost due to the wrong fuel gas, equipment or process flow. That's why it's important to have an experienced and reliable partner on your side - one who can offer you a comprehensive product range, first-class technology and in-depth process knowledge.
Reheating with acetylene saves time
Acetylene has proven to be an ideal fuel gas for reheating. The properties of the flame allow very fast and precise heating, which can save considerable time. LINDOFLAMM® burners from Linde take advantage of the superior physical and chemical properties that acetylene offers as a fuel gas.
LINDOFLAMM® burners for reheating
LINDOFLAMM® technology ranges from manually operated to fully automated reheating systems, all tailored to meet your requirements in terms of both cost and performance. Our LINDOFLAMM® burners are not only suitable for automation, but also offer cost-effective solution concepts that meet the highest safety standards. Our seamless offering ranges from solution concepts for acetylene supply and LINDOFLAMM® burners to gas management systems and support services covering everything from development to realization.
The benefits at a glance:
- Easy to apply - retains material properties after welding
- Allows welding of high strength steels in accordance with standards
- Reduces the need for finishing and treatment after welding
- Reduces the risk of hydrogen-induced cracking
- Use of acetylene as torch gas allows for shorter warm-up times
- Adaptation of torch selection to customer requirements
- Customized gas supply concepts
- Can be integrated into existing process chains
Full range from Linde
If you work with materials that need to be preheated and/or reheated, Linde can offer you solution concepts that perfectly match your individual requirements. You also benefit from our wide range of services, which accompany you from development to realization. Since our pre-heating and reheating concepts are part of our comprehensive LINDOFLAMM® program, we can offer you everything from manually operated to fully automated systems that meet your requirements in terms of both cost and performance.
Materials suitable for reheating include:
- Unalloyed and low-alloy steels
Hardware LINDOFLAMM® burner
Flexible and self-adjusting application for flame heating with LINDOFLAMM® burners
We have expanded our family of LINDOFLAMM® custom burners to give operators more flexibility and control during pre- and post-heating. LINDOFLAMM® Flexline comes with flexible hoses so operators can take advantage of new flame heating options that require precise heating in unusual or complex geometries.
The ergonomic design of the LINDOFLAMM® Flexline allows operators to quickly and easily adjust the torch configuration without outside assistance. This minimizes set-up and production downtime while operators wait for assistance. LINDOFLAMM® Flexline is a versatile and valuable addition to any LINDOFLAMM® burner system.
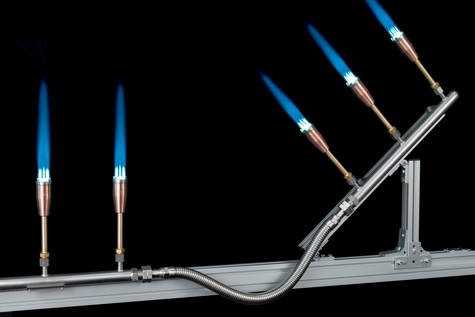
Image: Flexible hoses allow for precise and even heating of the most difficult geometries.
Flexibility
The operator can position the torches accurately and adapt them to changing workpiece geometries (e.g. pipe diameter) during machining. The flexible hoses make operation more user-friendly and simple, opening up new application possibilities.
Automation
LINDOFLAMM® Flexline is suitable for manual use and for automated processes.
Adaptability
Several LINDOFLAMM® burners can be combined to perfectly suit any flame heating task.
Time and cost savings
Costs can be reduced through flexible use and the resulting reduction in set-up times, production downtime and required burner systems.
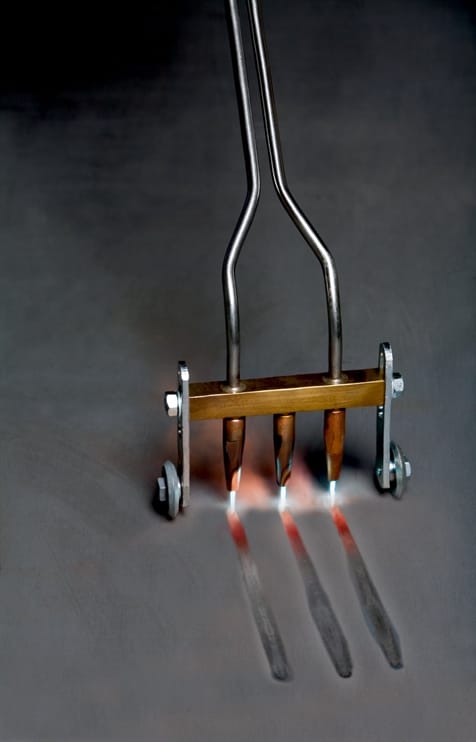
Flame straightening & training according to DVS guideline 1145
Correct weld deformation without affecting material properties
Welding and other fabrication processes that involve significant heat input can cause stresses in the workpiece, and during subsequent cooling, the workpiece can deform. Flame straightening is an effective, proven process for correcting weld distortion without affecting material properties.
Removal of deformations with an oxy-acetylene flame.
This process is based on the physical principle that metals expand when heated and contract when cooled. If they are obstructed in their expansion, stresses are created which lead to plastic deformations on subsequent cooling. To eliminate these deformations, a well-defined part of the workpiece is heated rapidly to flame temperature with an autoxy-acetylene flame. Materials for which this process is suitable include unalloyed and low-alloyed steel, high-alloyed stainless steel, copper, titanium and aluminum and aluminum alloys.
Ideal equipment for flame aiming
The appropriate equipment for flame pointing depends on the type of material and the material thickness of the workpiece. To complement our range of LINDOFLAMM® torches for standard straightening work on metal parts, we offer a range of LINDOFLAMM® special torches whose shape and performance we tailor to your individual flame straightening task. This makes these solution concepts ideal for workpieces with large material thicknesses.
The right fuel gas for flame pointing
During flame straightening, individual parts of the workpiece must be heated accurately and quickly to the correct flame straightening temperature. This is only possible if a high heat flux density occurs at the surface of the workpiece in a very limited space. Although a variety of combustible gases can be used for flame straightening, the highest flame temperatures and intensities for rapid heating are achieved with acetylene and oxygen.
The advantages at a glance:
- Easy to handle
- Eliminates deformation after welding or heating
- Often the only way to repair the product
- Most effective with acetylene as fuel gas
- Customization of burner selection to customer requirements
- Customized gas supply concepts
Materials suitable for straightening with the flame
All materials suitable for welding can be straightened with the flame without difficulty, if the specific properties of the material are taken into account.
- Non-alloy and low-alloy steels
- Highly alloyed stainless steel
- Galvanized parts
- Aluminum and aluminum alloys
- Copper, titanium
Service, training and customization at your premises
We can help you train your staff and design your gas supply system to best fit your specific application. One of our highly qualified application specialists can demonstrate to you on site how effective and economical LINDOFLAMM torches are used to eliminate welding distortion. Take advantage of our know-how as an approved DVS training center for flame straightening and blasting. Take the opportunity to qualify and certify your employees as specialists in flame straightening according to DVS Directive 1145.
Flame blasting & training in accordance with DVS guideline 1147
Vlam blasting is mainly used on steel structures, bridges, containers, but also on concrete, natural stone and wood
.Vlam blasting is used to prepare surfaces for the application of protective coats or coatings to protect against corrosion or other stresses.
There are basically three different areas of application:
- Descalation
- Rusting
- Flame phosphating
In descaling and de-rusting, the steel surface is chemically and physically prepared to be optimally suited to receive protective coatings. Flame phosphating applies a corrosion-inhibiting inorganic coating to a descaled and de-rusted steel surface.
Effective corrosion protection is achieved only if all interfering impurities, such as rust, boiler scale, old paint, all foreign matter and moisture, are removed prior to painting.
Flame blasting followed by mechanical brushing is a good way to achieve the desired cleanliness.